They are indispensable in many industries for different types of use, among which construction and electronics stand out. The durability, strength and flexibility of its design allow them to be used for multiple applications. But one issue which is true in almost all cases wehere these are involved, that’s rust problem. What we will be doing in this article is to offer a fact-based response to the question of whether sheet metal screws are rust-proof, together with discussing the materials made use of in making them and talk a little about discovering what the ideal screws are for your job. Frequently Asked Questions to Clarify on this topic
Sheet Metal Screws – What you need to know!
Sheet metal screws are available in various sizes and types, but they are designed to attach two pieces of sheet metal with a point at the tip that helps penetrate through metal. Available in a range of sizes and materials—stainless, carbon, coated. The material that their filter is made of, as this greatly affects if they can resist corrosion and rust. As such, stainless steel screws are a common example as they possess a natural resistance to oxidation.
American Iron and Steel Institute (AISI) defines stainless steel as a type of steel that contains at least 10.5% Chromium that forms an oxide layer on the surface to prevent it from further rusting. Meanwhile, carbon steel screws while tough, are quick to corrode unless they have been either coated or treated.
Rust Inhibitor Coating Just For You!
Manufacturers may coat sheet metal screws in order to increase their resistance to rust. Here are some common types:
1. Zinc Plating: An extremely common coating that forms a sacrificial layer to help prevent rust.
2. Galvanization: This process is stronger than zinc plating, as it fully immerses screws into hot liquid zinc and creates a thick cover around the meter screw.
3. Epoxy Coating – This provides some of the best chemical resistance for use in harsh chemical environments.
4. Stainless Steel: Like I said, stainless steel screws provide inherent resistance to rusting and don’t need a special coating.
The appropriate coating is largely dependent on the environment in which these screws are intended to be used. For example, a screw that will be underwater or in high humidity must be protected far beyond what would be needed for use indoors.
Case Study: Practical Examples in the Field
One example from a case study of coastal construction: Stainless steel sheet metal screws used on corrosion prone saltwater exposure. These screws only showed minor signs of tarnish over a two-year period, showing that they really are a great option for environments harsh on metal. Carbon steel screws installed in the same project, on the other hand quickly started rusting, resulting in structural concerns and expensive replacements.
At the same time, in an automotive industry case, it uses galvanized screws in their assembly lines. These screws worked to great effect in withstanding the effects of oils and chemicals, allowing the vehicles to last longer over time.
Common Questions About Rust-Free Sheet Metal Screws
But not all sheet metal screws are resistant to rust.
Not all sheet metal screws are necessarily going to be rust-proof. Rust Resistance: These pole construction guides are rust-resistant because of the material and coating. Stainless steel is more resistant to rust compared to an untreated screw quality out of carbon steel.
The Ideal Screw Type for Outside Areas
While building a pergola, Galvanized and Stainless Steel screws are ideal for outdoor use because they are more resistant to rust. The decision should also account for environmental considerations, like unabated moisture and corrosives.
Ways to Avoid Rust on Sheet Metal Screws
The use of appropriate materials and coatings, proper storage i.e. seal screws in air tight navy cloth to prevent rust formation, apply an anti-corrosion get on the screw point if needed. Furthermore, sub-optimal regular inspections can detect early signs of corrosion.
Wherever possible, industry professionals advise that the application environment should be assessed very well before the final choice of sheet metal screws is made. In the case of screws, things like high humidity environments, exposure to chemicals and fluctuations in temperature can play a huge roll in screw performance. It is also important to follow the manufacturer’s guidelines on how they installation and maintain the screws as well, as it will increase their working life.
NAM, or the National Association Of Manufactures, A dc based organization stresses for using quality materials and coatings as a part of fastening solutions. Spending more on quality screws initially can end up saving you as they will fail far less than inferior products.
Conclusion
These corrosion resistant properties are not usually inherent in the materials that sheet metal screws nor is it always due to the application of a specific coating. Stainless steel, and galvanized screws are ideal for corrosive environments; while carbon screws may need additional protection or would be better off indoors. With proper understanding of your project, and choosing the right screws, you enhance lastingness and reliability. With the right information in hand, you can ensure your installations will last and create countless potential repairs down the line.
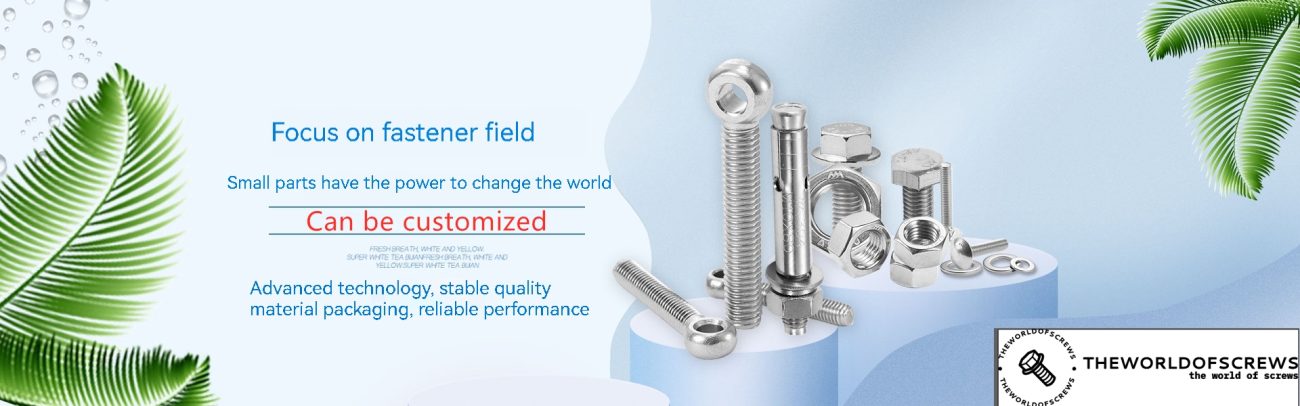