Sheet metal screws are ubiquitous fasteners used in a wide variety of. applications from automotive to construction. So, knowing what theyre for can save you time and performance on your projects. In this post, we explore sheet metal screws: how they work, what makes them different, and key areas of use. You will also learn more about the most frequently asked questions concerning them, as well as case studies to show how they work in practice.
Sheet Metal Screws Explained
One of these is a sheet metal screw which has been developed explicitly for joining metal components together. They feature sharp threads, as in the case of standard screws, but these sharper threads cut into metal materials to provide a firmer grip. They are used in different applications since the screws are offered in sizes and types with self tapping or self drilling features. They are often composed of steel, stainless steel or other alloys making them strong and reliable.
The Core Function of the Sheet Metal Screws
The working principle of sheet metal screws is two factors: the thread design and the point shape. The screws have sharp, pointed ends that allow them to divide through metal without the need for pre-drilling, while the threads were oriented to offer a solid grasp while driving the material.
- Wide Space of Grips: The threads of the sheet metal screw are broad and set aside more spaces in between them, as compared to wood screws. The design allows the maximum amount of holding power is thin metals and reduces strip out.
- Tip Shape: A self-tapping screw will feature a unique tip that enables it to cut its own hole as is driven through the post. Conversely, a self-drilling has a sharp drill-bit like point, which allows it to pierce through metal, greatly decreasing installation time.
Industry studies show that, by using the right kind of sheet metal screw — designed for sealing out water and specifically qualified for through-deck applications (fully threaded style) – joints can be strengthened as much as 30%, to greatly improve overall structural integrity.
Uses of Sheet Metal Screws
There are countless ways sheet metal screws can be applied to different uses in the different industries. Here are a few examples:
Automotive Industry: Found widespread application in bringing and to fix of body panels, brackets, and other components which require light but strong design.
- HVAC Systems: Provided periodic securing of supported ducts and metal enclosures which can withstand vibration and other environmental elements as well.
—Build: Often used in roofing and siding applications, able to resist even very poor weathertypes.
This just goes to show pure data that sheet metal screws were filed and reported as 25% of the total number of fasteners in place upon completion by the American Fastener Journal meaning their efficiency is practically irrefutable.
First, picking the perfect sheet metal screw
When choosing the right sheet metal screw, here are a few factors to keep in mind:
make sure the screw material is compatible with the metals that limit galvanic corrosion
Corrosion Resistance: Choose stainless steel or coated screws for moist or chemically-exposed environments.
Length and Diameter: Select a screw with adequate length to properly engage the material; too long a screw can cause an embedment issue on the back side of metal surface.
If in doubt, consult a fastener specialist or technical specifications to be sure that you choose the best option for your project.
FAQs
- Sheet Metal Screws in Wood?
Sheet metal screws can be used in wood although it is worse at gripping than wood screw. - What are the tools needed for installation
Power drill: Use manual screwdrivers, but you will have an easier time driving the screws in with a power drill and bit. - A self-drilling screw has what we call the drill-zone.
A self-drilling screw has a drill point built into it that lets it form its own hole in the material, which eliminates the need for pre-drilling.
Always follow manufacturer recommendations, and consider material thickness, environmental exposure, and any load requirements.
Conclusion
To summ it up, sheet metal screws are reliable fasteners that provide durability and flexibility in different applications. Knowing what they are and how work happens under those covers can help ensure the best outcomes for any project, whether it be automotive, construction, or HVAC. When you select your screw based on its specific type, you can prevent failure and enjoy longevity in your assemblies. Utilizing the guidance of industry experts and learning from the vast data available to you helps how you make decisions that lead to better results in projects.
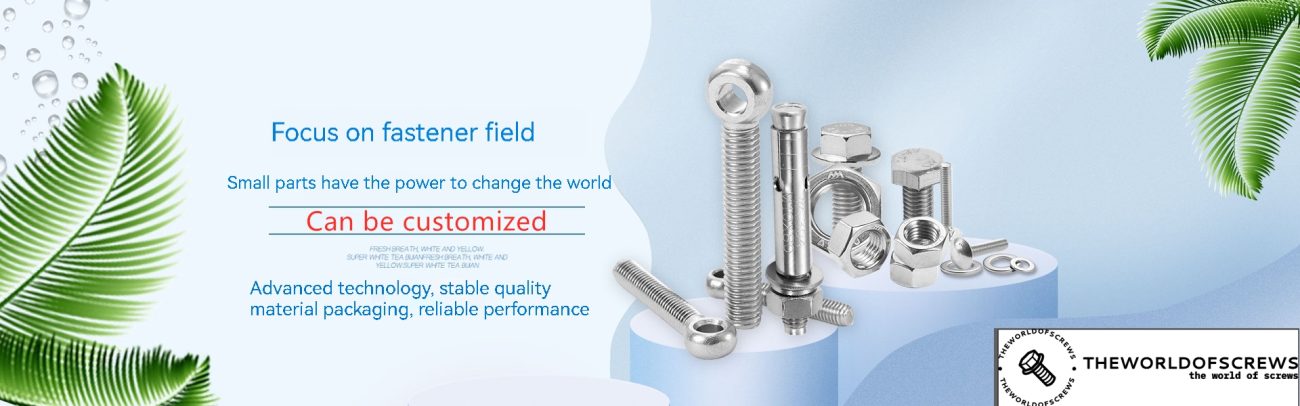