If you are in the construction, manufacturing or doing any DIY projects then identifying a sheet metal screw can be an important skill. Sheet metal screws are in a class of their own when it comes to fasteners as they were developed specifically for this purpose, setting them apart both mechanically and cosmetically. In this article, you can learn everything about sheet metal screws along with their application and how to identify them. Knowing these factors will help you to choose the appropriate screws for your work hence making them both durable and cost-effective.
Learn About Sheet Metal Screws
Sheet metal screws do an excellent job binding together thin sheets of metal. The tip is usually sharp which enables it to go through metal surfaces comfortably and the thread cut that aids in fixing into a metallic surface without needing a hole prior. Stainless steel, carbon steel and assorted other alloys allow for the screws to provide various degrees of strength and corrosion resistance.
There are several head types (pan, flat and truss) for sheet metal screws as well as drive styles so pay attention to what you’re looking at. This variation can affect the performance of screw in different applications. Just as one example, a pan head screw can be ideal when you need to have the weight of an object that is being fastened distributed over a broader surface area evenly.
TitleKey Identifying Characteristics
When trying to identify sheet metal screws, this is what you should look for:
- Type of Thread: Unlike other screws, sheet metal screws have very sharp threads which allow them to dig into the steel. This spacing—usually quite close together compared to wood screws—is critical to ensure you have maximum strength.
- Point Style: The pointed tip is necessary for drilled holes in metal; no pre-drilling needed In some cases, the screw is designed to be self-tapping and go right in with much less stress.
- Head Design: Specific head types are best suited to specific applications. Such as the type you see in a flat head screw that is designed for end on finishing and making it flush, or once again with another popular type called roundhead which gives an extra height to smooth out your work.
- Material Mix: This choice should be cross-referenced with the environment where they are to be used. For instance, stainless steel screws are highly resistant to corrosion and they tend to do well in outdoor applications.
- Size / Length: For the correct measurement of a screw, check its diameter and size to make sure it fits your requirement from your purpose. While standard sizes are widely stocked, custom lengths can be special ordered.
Applications of Sheet Metal Screws
Sheet metal screws are very common in nearly any application. Here are a few examples:
— HVAC System: The assembly of HVAC ductwork is frequently performed using sheet metal screws, and for good reason – they offer a reliable fastener that stands up to the repeated heating-cooling cycle.
— Automotive Industry: Sheet metal screws used by the manufacturer of vehicle assembly, especially in fastening body panels and many other parts.
— Appliance Manufacturing: Many white goods and electronic appliances are put together in an assembly configuration with sheet metal screws to hold the components securely.
— Improper fastening, especially in automotive and industrial applications can result in very crucial safety issues as per a study by the Fastener Quality Act. It demonstrates the need to choose a screw that is appropriate for its use.
Professionals Recommend for Sheet Metal Screws
Here are some tips from industry experts for choosing sheet metal screws:
Find the Load: Depending on how much weight and stress a joint will feel, use an appropriate screw size.
– For screws that will be wet, damp or exposed to chemicals choose stainless steel or coated screws as they won’t rust.
Use the Appropriate Tools : Have The Right Screw gun Bits And Drivers cause fastners for installation. When you use the wrong tool it can strip that screw head or even damage whatever material is on hand.
Test Before Full Installation: If at all possible, you should test a few screws in the material that it will be used on to ensure its performance before installing 5000 of them!
** FAQ
- Self-tapping vs. regular sheet metal screws: What’s the difference?
The screw has a sharp tip and drills its own hole in the material it is driven into, while normal screws need a pre-drilled hole. - Sheet metal screws in wood?
Loosly: Yes, sheet metal screws work in wood but do not hold as well as wood screws. - When do I use a coated screw?
Additionally, if your project will be exposed to moisture or harsh chemicals, take into account the use of coated screws which are available for increased corrosion resistance. - What do I need to install it?
You will need a power drill, appropriate size bits for drilling,, and correct style head on your screwdriver or driver bit.
Conclusion
Sheet metal screws all have their own distinct characteristics and applications, so this makes it a bit difficult to determine which one would work best for your project. This will help you to make some informed decisions about the quality and life of your work, through thread type head style and material composition. Screws are subject to the environmental considerations and loadings, so please choose them appropriately for a safe and untroubled interfacing solution. Now, with that information in your back pocket (like bobby pins and lint), you can easily execute any sheet metal screw project making yourself the expert that you are!
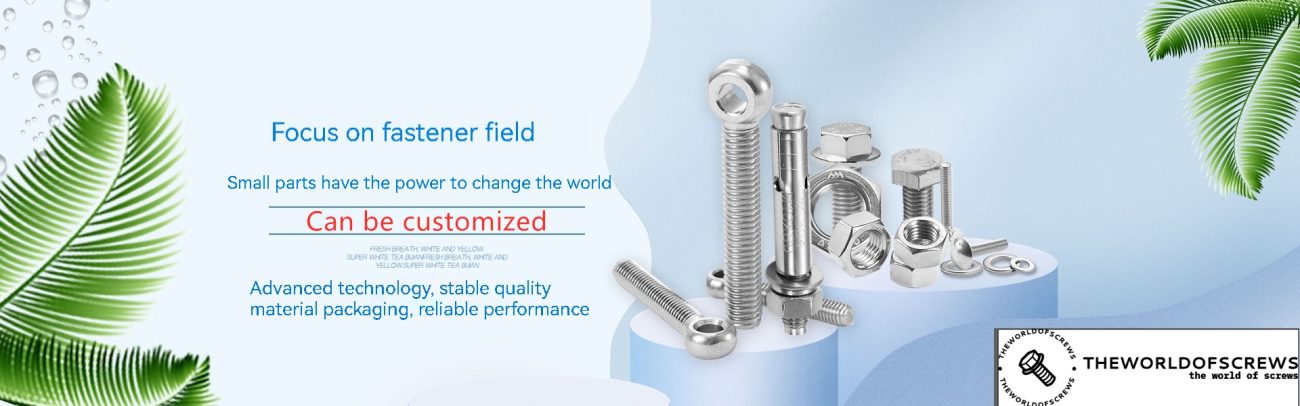