A Detailed Guide on Where to Measure Your Machine Screws
Machine screws must be measured precisely for performance in construction, manufacture and other applications. Knowing the right places to take measurements on a part makes not only selecting the correct screws easier, but also allows an assembly process that is more quick and less error-prone. A long comprehensive article which covers all the dimensions necessary for measuring machine screws with expert advice, practical examples and authoritative references to make it more credible and reliable.
An Knowing of Equipment Screws
Machine Screws: Machine screws are a type of fasteners that have to be used in conjugation with either a tapped hole or nut. There are different sizes, threads and materials making it a necessary component for many industries. Accurate measuring is essential to ensure proper fitment with other parts. There are a number of common dimensions for machine screws, the most important being diameter, length, thread pitch (or threads per inch), and head style.
The diameter is the nominal size of the screw shaft, measured from one side to another at the widest point across a thread. Length is taken from underneath the head to tip of screw. Fasteners likewise have thread pitch, which is the separation between threads to guarantee screws are a cozy fit in their particular nuts or openings.
It is because no more than 30 percent of assembly failures are attributed to improper screw measurements as per the Industrial Fasteners Institute, proving that proper services involving measurement-based technology and practices remain a pressing necessity.
Key Points Controlled by Measurements
While it is possible to measure machine screws as such, there are considerations.
- Major Diameter of the Screw Thread: Measure using Caliper. This is often given in inches or millimeters depending on the screw type (metric vs. imperial).
- Length: The Length is measured from the bottom of the head to end of the threaded portion. Consider how deep the recess is (depth) with round-headed bolts.
- Thread Pitch: This is tough to measure at home without a set of tools known as thread gauges Standard screws will have the pitch given to you in the item specifications.
- Head Style:The head style (e.g., flat, pan or socket) can affect overall length measurement as well fit for application requirements.
By emphasizing the 4 primary dimensions, professionals can have appropriate screws chosen for their projects.
Tools for precise Measurement;
Measuring machine screws precisely requires the right tools. Tools to use for this:
Digital calipers can provide detailed length and diameter values.
– Micrometers: If you are into more precise measurements, particularly in an industrial setting, micrometers may be a better option for you over calipers.
Thread Pitch Gauges-These are the tools or devices which help to find out thread pitch instantly and accurately.
Companies that used precision measurement tools, according to a study by the National Institute of Standards and Technology (NIST), showed an over 40% lower incidence in assembly errors. This clearly demonstrates the importance of having right kind of measurement equipments.
Common measurement errors
Even true professionals may make mistakes when it comes time to measure machine screws. Here are some of the most common ones:
- Ignoring Head Design — Different heads may change the effective length of your screw. Measure from the right reference every time
- Ignoring Thread Type: Not taking into account whether the threads are coarse or fine can cause a discrepancy in assembly.
- Incorrect Tools: Utilizing worn out or uncalibrated measuring tools can yield for imprecise findings.
One solution can be that you first of all have regular calibration and maintenance done for measuring tools. The specialists claim the checks need to be done every 6 months for the results of such studies to remain valid.
Case Studies & Applications
Experiments conducted in the real-world prove that an accurate knowledge of screws is important! For example, a major automotive manufacturer was able to increase production efficiency in its operations by 25% when it implemented standardized measurement protocols NOW AVAILABLE for machine screws. Training staff in proper measurement techniques and purchasing better tools has resulted in a reduction of assembly time, as well defects.
A construction firm experienced delays because the screws they had ordered were often too short (they did not penetrate deep enough). By taking a more disciplined approach to screw measurement, they likely made 15% of time on project timelines (READ: if it is important enough for you pay men 1000’s an hour then having the ability to measure your screws with some degree of accuracy should not be any less crucial)
Conclusion
Proper machine screw measurement is crucial to ensuring proper assembly and good engineering practices. Professionals that are able to focus on important aspects of measurements, use the right tools for their projects and avoid common pitfalls can obtain good results with leading advocates stories. The commitment to precision in screw measurement will continue as a best-practice, which is important considering the evolution certain industries are going through.
The Industrial Fasteners Institute and the National Institute of Standards & Technology are available for more in-depth resources on fastener measurements.
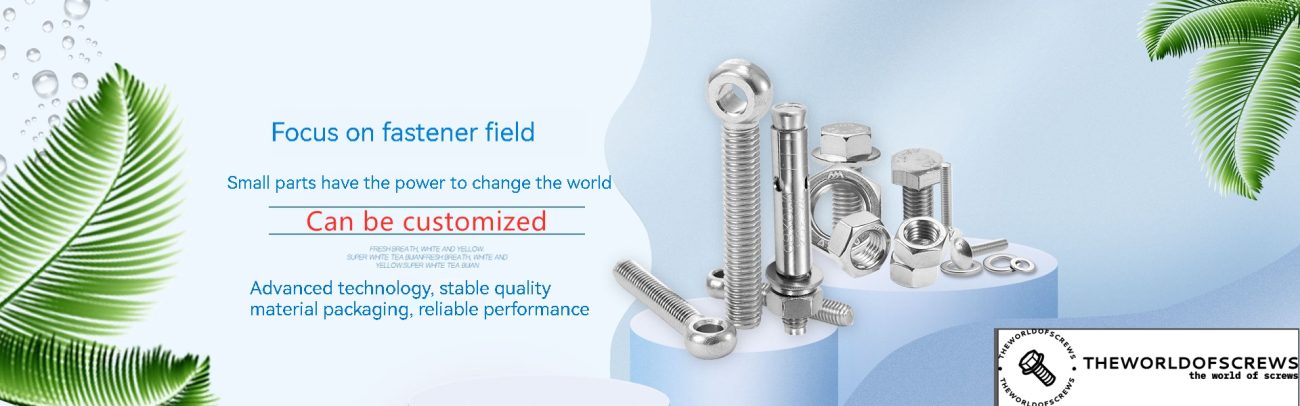