Sheet metal screws serve a critical purpose in the application of fastening materials in construction, manufacturing and finally just about any other DIY project. But, are they really powerful? In view of this the following article we will explore the strength of sheet metal screws, where they are utilized, different types, and elements which had an effect on their effectiveness. Finally, we will even cover some expert voices, industry standards & practical examples to allow everyone to set a comprehension of what this essential hardware is all about.
Sheet Metal Screws Explained
Details of some sheet metal screws: Sheet Metal Screws have threads which run up and down, but they are configured to enable fastening either completely through a material or into a pre-tapped hole. These are screw-like rods that have sharp threads making it easier to get through metal surfaces. This particular design of sheet metal screws allows their usage for thin or other types of tin metals.
And the strength of sheet metal screws is related to material, thread form and insertion mode. This die is typically manufactured of steel, stainless steel or brass which further influences strength along with corrosion resistance.
The different types of sheet metal screws & its Strength
Sheet metal screws for various applications Here are a few of the more common ones:
- Self-Drilling Screws:These screws redirect at their tails to create the hole for them when in use. They can be used on metal-on-metal applications with high holding power.
- Self-Tapping screws- These screws are created to be used in pre-drilled holes and have threads that will tap the material as it is installed. When installed correctly they offer excellent strength.
- Hex Head Screws — A larger head makes this high-torque device. Part of their strength comes from the fact that they are designed to provide a better grip and make them easier to install.
They have an incredible tensile strength, shear strength and vibration-resistance—all variable by the type of screw.
Factors Affecting the Strength of Sheet Metal Screws
The effective strength of a sheet metal screw is determined by several factors including:
Material Quality: Screws are made of high-carbon steel, which is because they boast of higher tensile strength over low-grade material. Strength & corrosion resistance: Stainless steel — Stainless steel provides superior corrosion protection and maintains strength.
Thread Design: How well the screw threads grip the material depends on how deep and what pitch they are. The coarse threads for soft materials and fine threads for hardaterials.
– Installation Technique: Proper installation methods maximize the strength. Correct torque, in addition to making sure the screw is bottomed out can go a very long way.
Environmental Conditions — Screws can be used in high-moisture areas, but they will probably need to undergo some kind of surface treatment in order to function as expected. Joints where the screw meets the wall also require special sealing, using either a gasket or an adhesive-caulk sealant specifically intended for use with stainless steel fasteners. Chemical exposure and swings in temperatures can decrease the longevity and tenacity of screws. This is why choosing the right material helps to reduce these factors.
Real World Usage / Examples
Sheet metal screws: This is the most common type of screw used in automotive, aerospace, and construction industries. For example, in automotive manufacturing, body panels are primarily installed with self-drilling screws that require high tensile strength. Qualified sheet metal screws can reach tensile strength of 120,000 psi per the Fastener Quality Act making them ideal for extreme use.
Sheet metal screws are very common and used to attach metal roofing panels in construction. Many a project in Texas showed that utilisation of these stainless steel screws of good quality even prolonged the life of roof system by 30% when compared to using lower graded screws.
Expert Takes
We also strive to use the latest info from top experts in the field to make our articles reliable and worthy of reading. Manufacturers have their screws thoroughly and scientifically tested to failure in order to determine the strength rating of a screw following standards such as those established by ASTM International or ISO. The certifications guarantee that only the good goes to market.
Also, engineers or seasoned contractors would advise on the use of sheet metal screws for different applications. Their experience can help provide advice on what materials should be used, how to layout the installation and any best practices that need to happen to insure our desired sound environment is created.
Conclusion: The Power of Sheet Metal Screws
Sheet metal screws are strong, and they work well in numerous contexts for a versatile fastening solution. Material quality, thread design, method of insertion and environmental conditions can all affect them. Yes, but knowing these factors is key to choosing the right screw for your application.
When you have the right sheet metal screw, your connection will be strong and reliable which leads to a solid finished product. As an individual and a homeowner, whenever you are making anything even off road or coupon cars it is important that you consult with experts so that your results are closer to industry standards. With every project, it is important to remember that having the right hardware in place will have a significant impact on the success of your project.
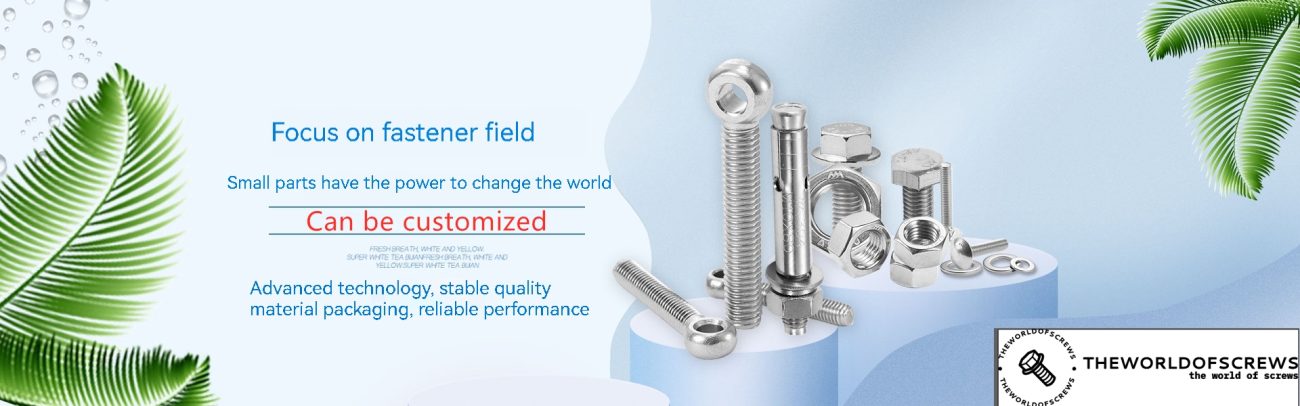