Sheet metal screws — the fasteners that are crucial for a multitude of applications, including those in the construction and automotive industries. Knowing about the manufacturing process of these screws will not only inform you how crucial they are but also show all related precision and technology behind their production. In this article, we are going to give you a detailed understanding of how sheet metal screws are made from the materials used in making them to its manufacturing followed by quality checks and usage. At the other end you will have more at hand to understand this critical part of it.
Materials for Making Sheet Metal Screws
Sheet Metal Screw Production Process There are a variety of raw materials used in the manufacture of sheet metal screws. Usually, these screws are steel, stainless steel or other regular alloys.
Steel: These are often coated with zinc for corrosion protection.
Stainless Steel – Has excellent corrosion characteristics that make it good for outdoor applications.
Brass and Aluminum: This materials is often used for lighter applications or aesthetics.
–The primary determinant of the strength, durability, and application suitability of the screw is the material. For instance, with stainless steel tensile strength can span from 70,000 to 220,000 psi according to the American Iron and Steel Institute (AISI), a range that makes it strong enough for challenging conditions.
The Manufacturing Step of Sheet Metal Screws
The manufacturing of sheet metal screws involves a few main steps, which include:
- Wire Drawing Step 1: The first step involves drawing steel wire from larger stages into thinner strands. In this way, a wire diameter is assured to meet the specification appropriate for different screw size.
- Cold Heading — The wire is then cold formed into the shape of the head and heated for temper. This can make the material stronger by work hardening.
- Thread Rolling : It is process in which we do not cut the threads, as it can make your screw weaken, so thread rolling(swaging) machanism used. This technique rolls a given screw to the die that forms the threads without removing material, any structure is not lost in this case.
- Screws are often subjected to heat treatment to increase hardness and strength In order to do so, metal may need tempering which changes the structure of the metal.
- The Plating and Coating: Last but not least, screws are covered with materials like zinc or some other finishes to avoid corrosion. Plating not only gets a protective layer to the screws, but also enhances the beauty of the screw.
Information provided by the industry suggests that screws with a proper coating can last as long as 50 years in the environment increasing the potential life of structures they are associated with.
Integrity Checks
When making sheet metal screws, quality control is very important. Several tests are performed on every batch to comply with industry standards. Quality assessments commonly include:
Tensile Strength Testing: This indicates the maximum stress that a screw can bear before failing.
§ Corrosion Resistance Tests: Screws are salt-sprayed to evaluate corrosion-resistance for the life of screws in corrosive surroundings.
Dimensional Inspections: automated systems inspect the size of screws to ensure they meet the required tolerance range.
A compliance to Local/International quality standard can reduce product defects up to 90% (ISO), So far your specific industrial applications have highest reliability on performances.
A number of industries utilize sheet metal screws including:
Construction- Nails — these are an important item for putting sheets of metal, wood or plastic together, allowing strong joints.
– Electronics: Sheet metal screws are used to prevent the components from falling off of electronic devices, they need to be corrosion free for this purpose.
Automotive : These screws are used in the bonding of parts for safety and performance of vehicles.
Take the automotive sector for example — over 10 billion screws are believed to be used every year in car manufacturing and assembly.
Expert opinions and Credibility
Manufacturing of sheet metal screw is a skilful work and demands knowledge in the field of metallurgy, leverages, principles. Manufacturers will employ engineers trained in material sciences to optimize the screw designs for different applications. Moreover, industry certifications like ISO-9001 prevents quality management and continuous improvement.
For instance, companies such as Fastenal have been successful in the fastener industry by following strict guidelines and investing in advanced manufacturing protocols. This is the reason why they have been able to garner faith of clients from so many verticals due to quality and innovation.
Conclusion
Manufacturing sheet metal screws is a complex process, which involves advanced manufacturing techniques and meticulous quality control procedures. Each step, from the selection of materials to coatings for final protection work together making these screws long-lasting and reliable for their defined applications. Understanding how these screws are made gives an insight into their importance in day-to-day products as they play a significant role in fields like construction, electronics and more. Spend quality dollars on sheet metal screws and improve the efficiency of projects, as well as enjoy experienced longevity.
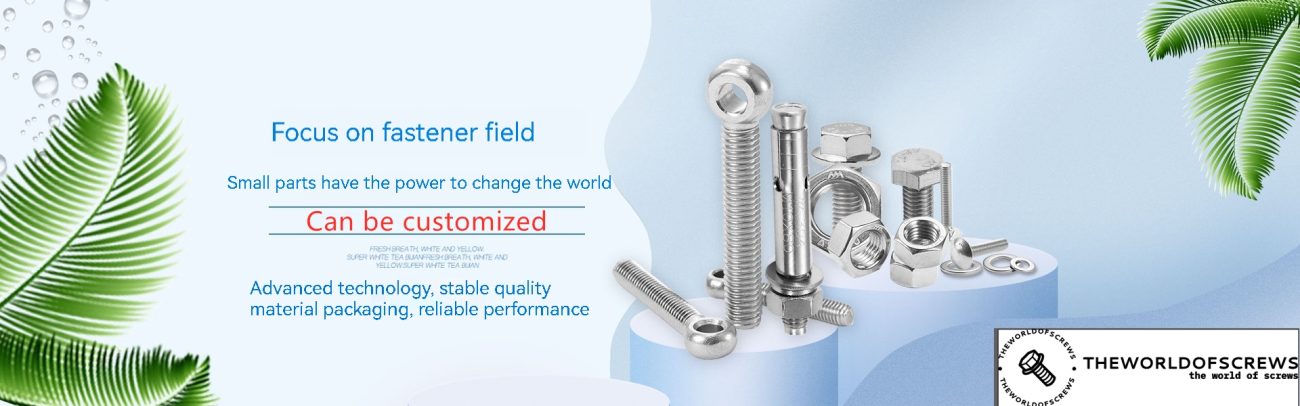