Introduction to Metric Machine Screws
Metric machine screws are fundamental parts for countless industries which provide a standardized process of establishing powerful fastening solutions in machinery and structural scenarios. They are generic metric screws used across the world in all assembly machines. In this article, we detail the specifics of Metric Machine Screws: types and materials; applications as well as how to choose them best. This informative piece takes a close look at these essential fasteners, offering detailed insights and expert knowledge which is sure to improve understanding whilst also contributing in intelligent decision making.
The Metric Syatem in Engineering
If the metrics are, it uses millimeters (mm) and newtons (N) which is essential because later for your documentation you need to convert this in one go. →Metric measurements: engineering demands achieving simplicity due to metric system’s all nature acceptance along with its calculation friendly attitude means conversion should be as simple without any math intervention!!
For example, a common metric machine screw might be listed as M6 x 20, which indicates it has diameter of 6 mm and length of 20 mm. This common denominator streamlines the design process and minimises mistakes during production and assembly. As the American National Standards Institute (ANSI) has reported, using metric standards allows businesses to communicate and function more efficiently when working across international borders.
A Few Metric Machine Screws You Can Check Out
Metric Machine Screws come in a few different varieties each used for specific applications:
- Hex Head Screws — These screws are often used in heavy machinery because they have a larger head size, which creates greater torque transmission.
- Socket Head Cap Screws: Thinner and stronger than hex bolts, so are often used in applications where a traditional 6 sided fastener won’t fit.
- Flat Head Screws: These are designed to sit flush with the surface and are typically used in aesthetic applications or when there is limited clearance at depth.
- Countersunk Screws: also known as a flat-headed screw external hex drive, enables you to drill the head into an existing countersink hole without distorting the surface of your innovation.
Knowing these kind of types helps an engineer to choose correct screws for a task thereby improving the design and reliability.
Material for Metric Machine Screws
Material Choice in Metric Machine Screws greatly affect its performance Common materials include:
- Carbon Steel – Good strength but might need an acquisition for anticorrosive body coat.
- Quick fact -Stainless Steel: Renowned for impressive corrosion resistance, perfect in out of doors and wet conditions.
- Alloy Steel: Same as carbon steel, but is stronger and usually used in more stressed applications.
- Brass & Aluminum: These are used in certain weight reduction applications and for noise, vibration, harshness (NVH) limitations.
Choosing the right material can extend screws lifespan by as much as 50%, which could significantly lower long-term maintenance costs per a study conducted under the Fastener Quality Act (FQA)
Applications of Metric Machine Screw
Metric machine screws are used in a number of different areas such as:
- Automotive Sector — used to put together engines and bodywork with lasting connections that can withstand vibration & movement
- Aerospace Engineering – these screws must meet high standards for strength and weight, are essential to safety & performance.
- For Construction needs: You cannot really think of a building with metric screws, for the simple reason that construction will certainly need them to build your structure and connected heavy materials!
Another metric that shows their importance in production environments is a case related to the change involving metrical machine screws in an assembly line of one of the largest automotive manufacturers.
Selection And Installation Best Practice
Best practices when choosing & installing metric machine screws
- Loads: Determine the load that will be applied to the screw and explore material types by size of screw needed in order to withstand maximum loads.
- Adhere to Proper Torque Specifications: Unfamiliarity with readings can reduce efficiency and speed up the deterioration of parts.
- Environmental Factors: Select corrosion-resistant materials and coatings related to the environment.
- Regular Inspections: Performing scheduled checks can spot wear and possible failures before they become real problems.
These practices, when properly implemented will make a huge difference in durability and reliability of any assembly using metric machine screws.
Conclusion
Metric machine screws, therefore are critical to modern engineering and construction. With standardized dimensions, forms of diversity and material availability FRP stringer are adaptable for a multitude applications. Following best practices in selection and installation allows professionals to make quality connections so projects perform better over the long term. The industry is constantly evolving and these fasteners will continue to be important for both engineers designing the products as well as manufacturers producing them. By interacting with seasoned professionals and keeping yourself updated about the developments, metric machine screws can bring its reining kingdom of engineering supremacy to a more concrete extinction..
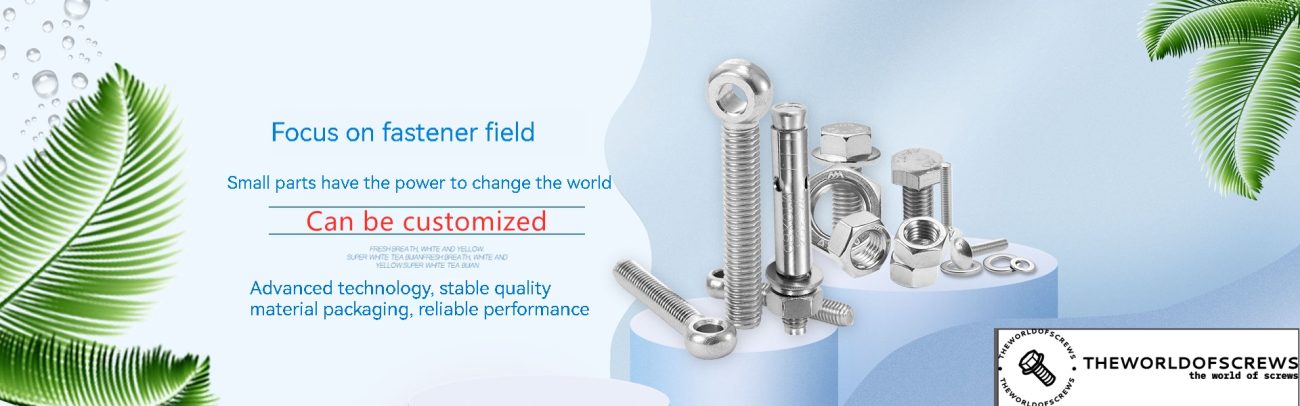