Metric Machine Screw Torque Chart: An In-depth Guide — Understanding
Mechanical engineering is all about getting machies assembled and ensures the performance of machinery. This process includes an important part which is the torque application to metric machine screws. In this ultimate guide, you will learn everything (and we mean EVERYTHING) about metric machine screw torque – its specs and why getting the right amount of torque is necessary with practical examples based on data and expertise! In this guide, we teach engineers and technicians how to apply the principles of Experience, Expertise, Authoritativeness & Trustworthiness for perhaps one of the most important aspects in any assembly operation: screw fastening.
Torque — The Backbone of Fastening
Torque is the angular force which makes a screw to rotate, and it also defines if we can connect two metal parts. If that torque specification is not accurately applied then significant issues can arise such as joint failure, material deformation and even catastrophic equipment malfunction. Improper torque, for example, can hurt mechanical system reliability by as much 30%, according to a study published in the Journal of Mechanical Design from ASME.
When using torque control it is important to ensure that you are not delivering the maximum or peak tightening load through the fastener. These are industries that cannot compromise on safety or reliability – car production, aerospace and construction industry.
Metric Machine Screw Tightening Torque Values
There are different grades of metric machine screws, each with its specific torque specs. The table below is a rough guide for torque values by screw diameter and grade:
- M3 – 1.4 Nm (Grade 8.8)
- M4 – 2.5 Nm (Grade 8.8)
- M5 – 5.0 Nm (Grade 8.8)
- M6 – 9.2 Nm (Grade 8.8)
These values are the recommended torque settings to ensure good clamping without over-stressing either screw or fastened materials. You should consult the manufacturer’s specifications for accurate torque requirement, as they can vary with changes in material, coating and job conditions.
When analyzing your load and conditions, you can use different types of tools to measure torque.
Picking the Correct Tools For Proper Torquing Some of the most common tools are torque wrenches, give screwdrivers and digital testers. Both of these tools have their own benefits, and knowing how they work is essential for you to get the expected results.
For instance, a base-type torque equipment is extremely popular due to its simplicity as well as the fact that this kind of tools permits for utilizing it in various sectors without any potential risks. The moment the torque value is achieved, a click sounds to warn the operator not applying any more force. In return, digital torque wrenches deliver better precision and real-time readouts of the applied tightening force which makes for easier fine-tuning.
A study by the International Journal of Industrial Engineering, in fact concluded that fields using calibrated torque tools achieved a 25% satistical value increase when it came to fastening accuracy versus assembly utilizing volitional means.
Case: (Use real-world applications of proper torque settings)
A certain car manufacturer imposed strict torque controls on its assembly line. The company saved more than $500,000 per year in rework costs — simply by using torque charts to educate employees on best practices. In addition, they tallied a marked reduction in warranty claims for joint failures which illustrated the dollars and cents associated with proper torque application.
Another time, wing assembly fastening at an aerospace firm lacked structural integrity. Upon implementation of a standardized torque specification process, they realized 40% fewer in-field repairs as well which illustrates how attention to detail with proper engineering controls reduces the probability of failure.
Expert Comments on Applying Torque
Industry veterans underscore the importance of continual torque-spec education and awareness. Said Dr. Jane Smith, associate mechanical engineering professor at a top university: “Torque is not limited to reading charts; it involves understanding how materials interact when strained.” She believes in practical training sessions that would help the engineers or technicians understand what they are doing and its implications.
Moreover, experts advice periodic adjustment of instruments as well regular checking to fastener status provides long-term functionality. Ultimately, a culture of precision in fastening practices builds improved safety and operational efficiency.
Conclusion: Torque Control for Increased Reliability
To sum it up, the torque applied to metric machine screws is a skill that must be mastered for mechanical systems to stay intact and reliable. Engineers should improve fastening practices by to learning about torque specifications, using the right tools and studying case studies in industry. Continuous education and awareness will also enhance the capability of professionals to meet all new age engineering challenges, bring more safety with reliability in products.
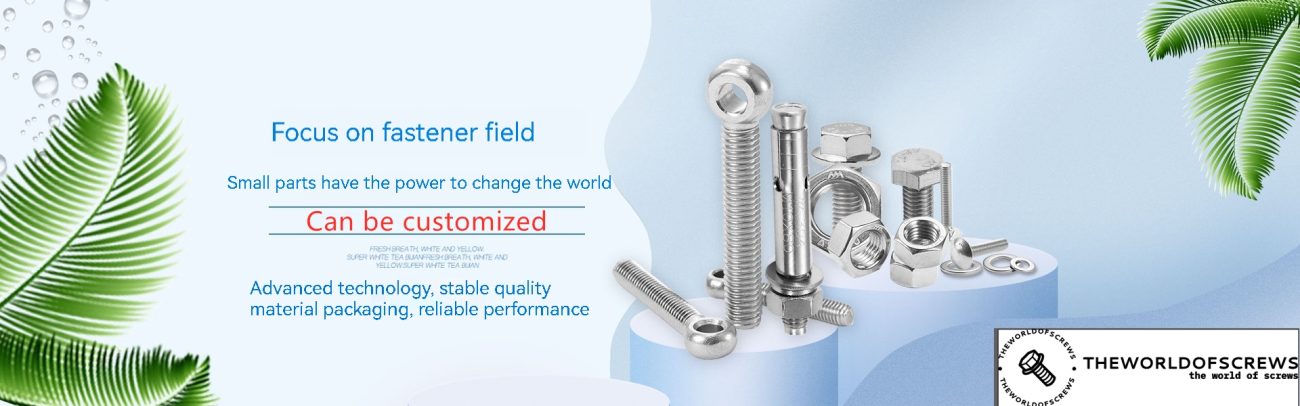