Sheet metal screws are multi-application fasteners primarily used for joining together different material — most often, to join sheet metals and plastics. Thanks to their patented thread pattern, they can be inserted effortlessly into thin sheets for a tight grip without surface damage. To put that human factor into a proper perspective, let us explore different uses and types of sheet metal screws in this write-up.
Sheet Metal Screws: An Overview
Sheet metal screws have a sharp, pointed tip that allow them to be easily inserted into sheeted surfaces as well as other materials. The fasteners of cap screws are known for coming in several sizes, lengths and head styles, which make them a reliable choice that has been designed per suitability across the multiple applications. These screws can be coated with corrosion-resistant coatings and are commonly made out of steel, stainless steel or brass.
More than 100 billion screws are used each year just within North America (Industrial Fasteners Institute)
Uses of drywall screws – Sheet metal screws
Sheet metal screws are used in the automotive, aerospace and construction industry. Some most common uses are as follows:-
HVAC Systems — This is a common way to connect ductwork that allows the system connection to be air tight and helps improve efficiency.
·Electrical Enclosures: Sheet metal screws are often used in electrical applications to secure the panels and covers that safeguard sensitive device components from environmental factors.
Automotive Manufacturing: Car manufacturers use sheet metal screws to connect body panels and other parts because of their robustness and dependability.
– Sheet Metal Screws: When it comes to metal fabrication in custom metal projects, sheet-metal screws are perfect for joining two pieces of ready-cut metals or creating your own parts from scratch.
According to a recent Fastener Technology International study, almost 70 percent of manufacturers favor sheet metal screws when they need a long-term hold on thin materials.
Sheet Metal Screws That Are Available nowadays
To assure proper function, you will need to choose the correct type of sheet metal screw. Some common species are listed below:
– Self-Tapping Screws: These screws can create there own hole in the material as they are driven Perfect for rapid assembly without having to pre-drill.
– Self-Drilling Screws: These screws have a drill point in their tips that penetrates thicker materials without pilot holes, ideal for general applications
Thread Cutting Screws: Made for applications in softer materials, these screws cut threads into the base material as they are installed to yield a secure connection.
There is purpose behind each type, and choosing the right one can have a big impact on how long lasting the connection will be.
Sheet Metal Screws: Benefits
The benefits of sheet metal screws go further than simple joining:
Strength: They anchor core structure provides great holding power making them perfect for heavy load applications.
Corrosion Resistance- A lot of sheet metal screws come with a finish such as zinc or an epoxy and they will protect the screw from rusting off, giving you many years out of your assembly.
Ease of Use: They have a sharp point and are available with different drive style like phillips or hex so they can be installed —or even removed— easily saving you time.
In fact, research from the Fastener Quality Act suggests that correctly installed sheet metal screws can last 25 years under normal conditions so there are some benefits to a few generations old mechanism.
Sheet Metal Screws: Selection and Installation:
When selecting and setting sheet metal screws, you should assimilate some rules:
Material Compatibility: Make sure the screw material matches the application environment to avoid galvanic corrosion.
Length and Diameter: Choose the screws that fit with thickness of materials to join. If you use a screw that is too long, it can damage what’s under the surface layer; if it is too short, there will not be enough to hold.
Installation technique: Applying the proper torque settings to avoid shearing or damaging of materials. Using a torque wrench would allow you to apply pressure and know how much is enough without overtightening the bell.
According to expert recommendations, making a pilot hole will provide for accurate and low-stress screwing on thicker materials.
Conclusion: Why Sheet Metal Screws Are the Best
Overall, sheet metal screws are the relevant fasteners that can be used in current manufacturing and structure providing mobility, reliability resultant. Knowing more about where they should be used and different types of rasterization algorithms will help improve the quality of your projects. When selected and installed correctly, these fasteners offer years of reliable service which is why industries everywhere rely upon them. By adhering to do standards and availing the expert knowledge you can make your assembly process world class quality & safe.
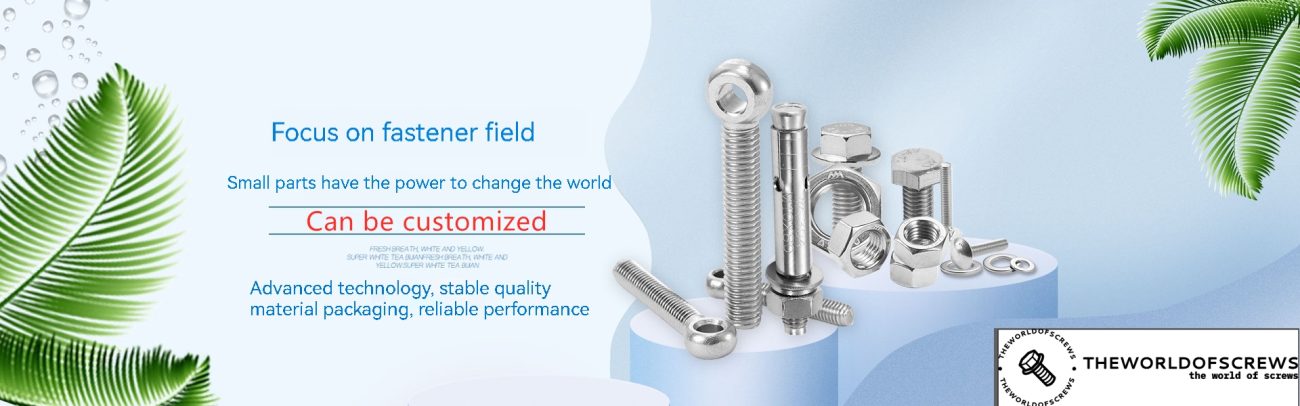